Chemical safety training is vital for protecting yourself and your coworkers from accidents, injuries, or fatalities. Proper training helps you recognize hazards, follow safety protocols, and use protective equipment effectively. It also guarantees compliance with regulations, reducing legal risks and potential penalties. With ongoing education, you stay updated on safety standards and improve risk management. Keep exploring to discover how effective training can transform your workplace safety culture and prevent disasters.
Key Takeaways
- Effective chemical safety training reduces workplace accidents, injuries, and fatalities involving hazardous substances.
- Proper training ensures compliance with OSHA, GHS, TSCA, and other regulations, avoiding legal penalties.
- It enhances hazard recognition skills, enabling employees to identify and mitigate chemical risks proactively.
- Safety training improves emergency response preparedness, minimizing environmental and property damage.
- Ongoing education fosters a safety culture, encouraging shared responsibility and continuous risk management.
The Frequency and Risks of Chemical Incidents
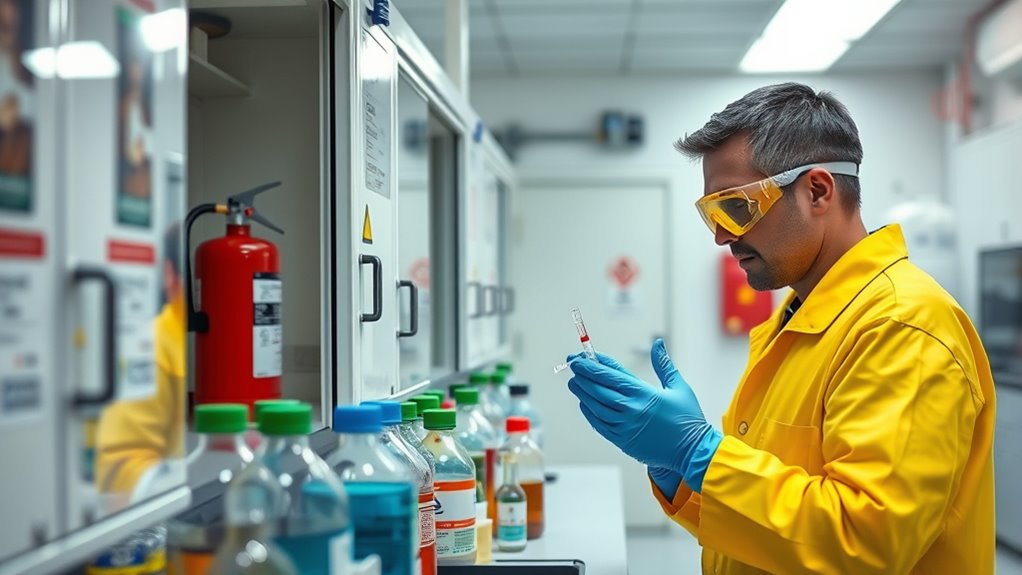
Chemical incidents happen more often than many realize, posing serious risks to workers and nearby communities. In 2025 alone, the U.S. Chemical Safety Board documented 26 incidents, highlighting how common these events are. These accidents can lead to fatalities and serious injuries—five deaths and 17 injuries in recent reports—showing their severity. Property damage costs skyrocket, with estimates reaching $700 million. Environmental impacts also threaten ecosystems and public health. Approximately 140,000 workers die annually from occupational hazards, including chemical exposures, emphasizing the ongoing danger. Understanding personality traits such as resilience and emotional intelligence can help in fostering a safety-conscious mindset among workers. As a worker, you face the real danger of exposure, long-term health issues, or even death. These incidents underscore the critical need for safety measures, proper training, and strict oversight to protect everyone involved.
Key Metrics for Evaluating Training Effectiveness
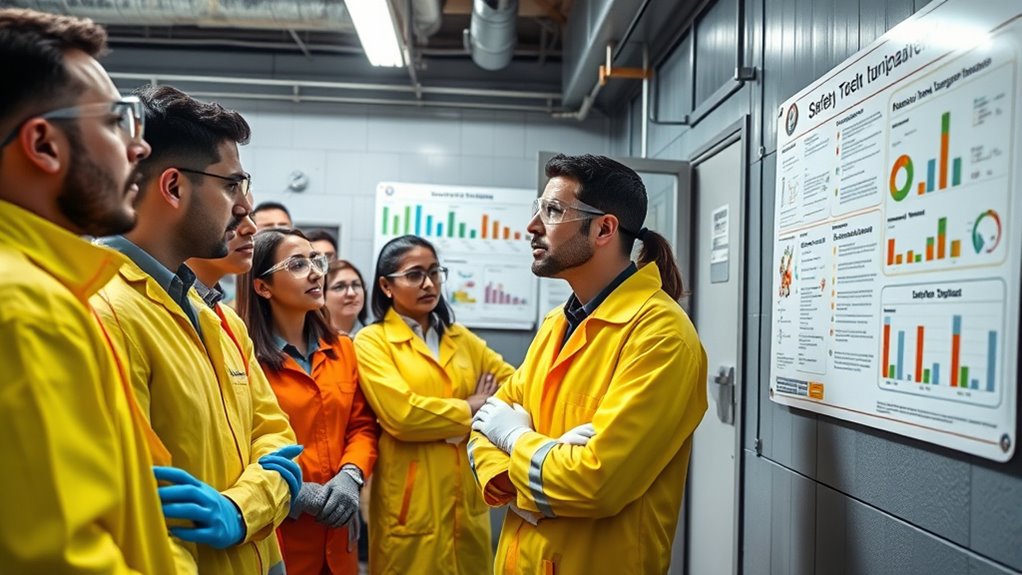
To determine whether safety training effectively reduces chemical incidents, you need reliable metrics that measure progress and impact. You should track KPIs like incident rates and compliance levels to see if safety improves over time. You can also incorporate training retention assessments to evaluate how well employees remember safety procedures after completion. Pre- and post-training assessments provide valuable insights into knowledge gains and retention among employees. Monitoring emotional responses during and after training can also help identify areas where employees may need additional support or clarification. Toxicity monitoring helps evaluate whether exposure risks decrease after training. Analyzing incident records before and after training reveals tangible safety improvements. Regular compliance audits ensure workers follow safety regulations consistently. Additionally, monitoring training engagement—attendance, participation, and feedback—provides insights into how well the material resonates. Safety protocols and their adherence should also be evaluated to ensure comprehensive safety practices are being followed. Implementing effective communication strategies can further enhance understanding and commitment to safety procedures. Incorporating sound science into training methods can improve the effectiveness of safety messages and techniques. These metrics collectively help you assess if your training program reduces chemical hazards and promotes safer practices. By focusing on these key indicators, you can identify areas for improvement and demonstrate the value of your safety initiatives effectively.
Improvements in Workplace Safety Measures
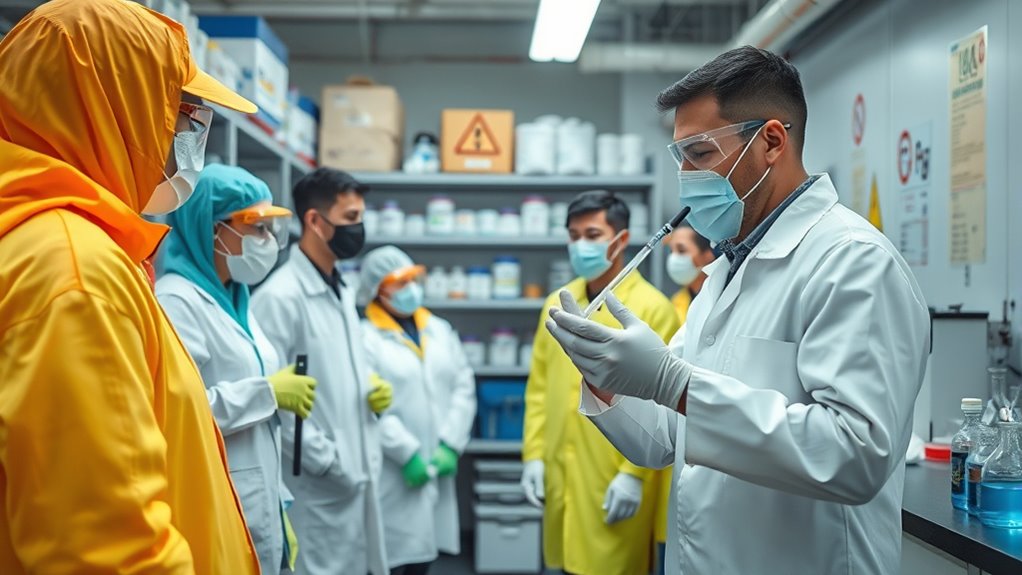
Advancements in workplace safety measures are transforming how organizations protect their employees. Regulations like the OSH Act and Mine Safety Act have strengthened safety standards, saving over 712,000 lives and improving conditions across industries.
Updated regulations now emphasize data transparency and global compliance, ensuring consistent safety practices. Technology plays a vital role, with automated safety systems, data analytics, and digital training platforms making safety monitoring more effective and accessible.
Innovations in PPE enhance worker protection and comfort, while risk assessment software helps identify hazards proactively. Additionally, fostering a strong safety culture—through violence prevention, mental health support, and employee engagement—creates a safer environment.
These improvements collectively reduce injuries, boost productivity, and reinforce your organization’s commitment to safeguarding everyone on the job.
Enhancing Knowledge Retention Among Workers
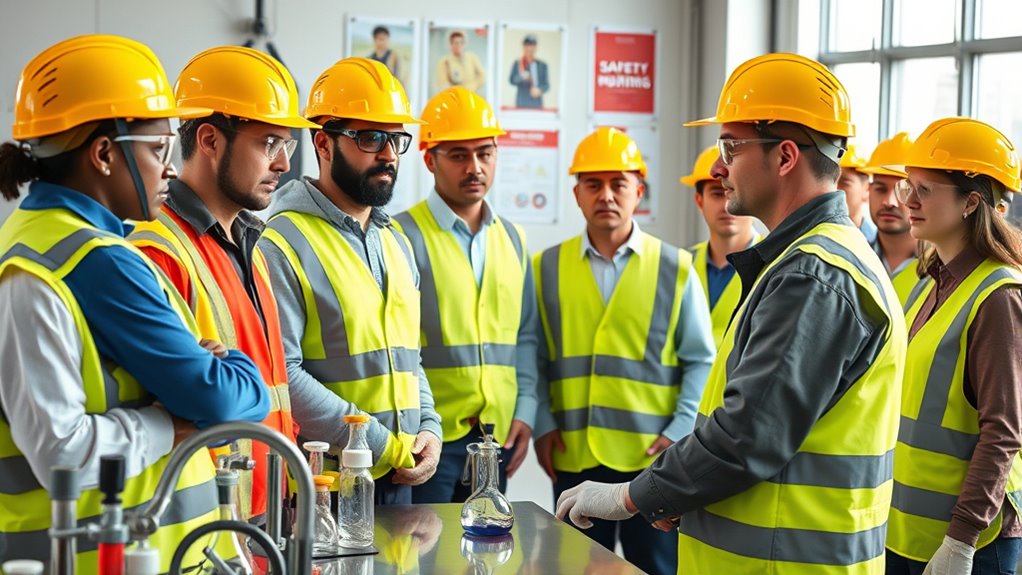
Enhancing knowledge retention among workers is essential for maintaining a safe and compliant workplace. Without reinforcement, up to 70% of safety content can be forgotten within 24 hours, making it crucial to use active learning methods. Stress can speed up forgetting, so engaging workers through hands-on practice and real-world simulations helps solidify protocols. Incorporating group problem-solving, storytelling, and peer discussions to improve recall is also effective. Frequent repetition, such as microlearning modules and monthly refresher courses, prevents skill decay and habit formation. Using technology like gamified quizzes, mobile checklists, and digital dashboards further reinforces safety practices. Immediate feedback and ongoing coaching ensure that safety knowledge sticks, reducing risks and fostering a safety-first culture. This multi-faceted approach keeps safety procedures fresh and effective. Additionally, utilizing exfoliation techniques can assist in maintaining healthy skin, emphasizing the importance of consistent safety and health practices in the workplace. Understanding environmental considerations helps in implementing sustainable camping practices that protect local ecosystems. Furthermore, understanding Kia Tuning options can help ensure that vehicle modifications are performed safely and correctly, reducing potential hazards. Incorporating diverse plant designs into workplace wellness programs can also promote a healthier environment and boost morale. Leveraging AI-driven content clusters can optimize safety training programs and ensure comprehensive coverage of critical topics, making safety initiatives more effective.
Organizational Changes Driven by Safety Training
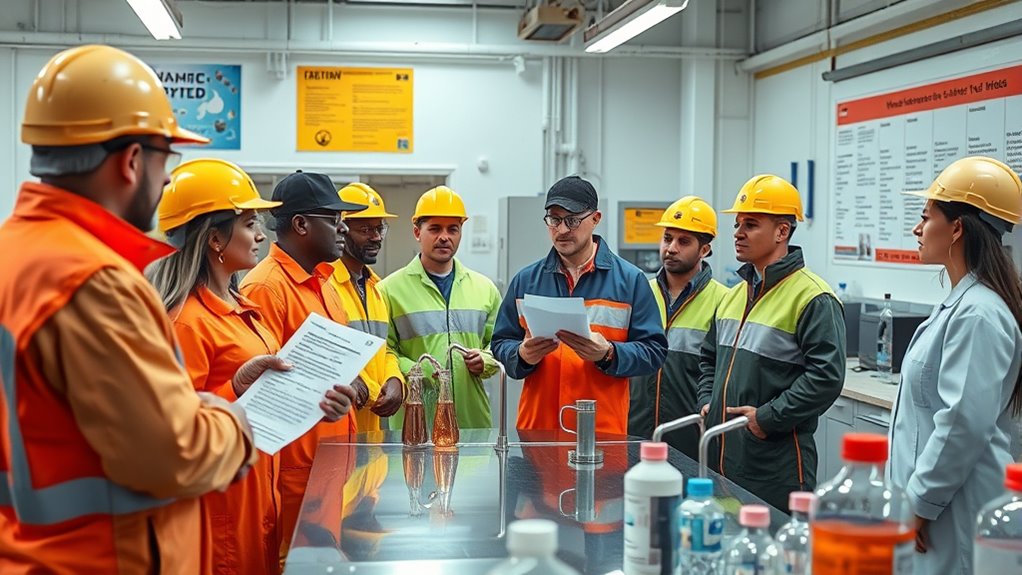
Implementing effective safety training can substantially reshape an organization’s culture around chemical safety. You’ll notice increased employee engagement and a stronger commitment to safety protocols. It fosters a peer-to-peer accountability and support system, encouraging everyone to prioritize safety.
As safety becomes ingrained, your organization adopts a more proactive safety mindset, reducing reactive responses to hazards. Incorporating safety training into onboarding processes ensures new hires understand safety expectations from the start. Additionally, emphasizing hazard recognition during training helps employees identify potential risks early, further strengthening safety practices. Developing a creative practice mindset can also inspire innovative approaches to hazard mitigation and safety improvements. Utilizing textile line techniques in safety communication materials can enhance engagement and understanding. Incorporating all Waterparks themes and visuals into safety training materials can make the content more relatable and memorable for employees. Integrating best practices from proven safety training methods can further elevate organizational safety standards.
Leadership involvement plays a pivotal role in driving cultural shifts, signaling safety’s importance at all levels. These changes promote a shared responsibility for safety, making it a core value.
Over time, this cultural transformation enhances overall safety performance, minimizes risks, and creates a safer, more resilient workplace for everyone.
Addressing Challenges in Chemical Hazard Management
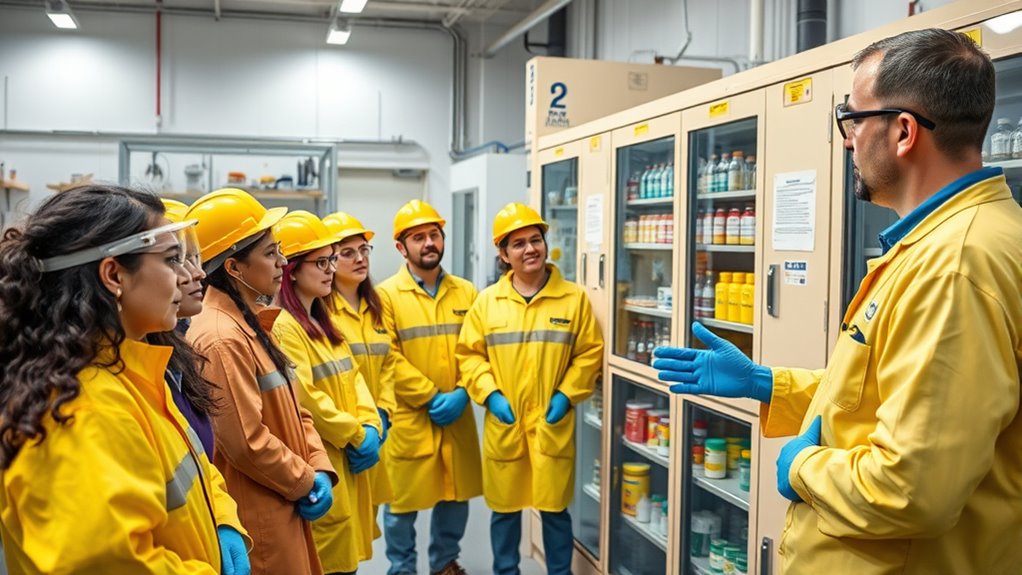
Managing chemical hazards effectively remains a significant challenge for organizations, especially given the complexities of maintaining accurate inventories and up-to-date Safety Data Sheets (SDSs). With over 900,000 chemicals used daily in U.S. workplaces, tracking these substances becomes overwhelming.
Nearly 40% of safety professionals cite inventory management and SDS updates as primary hurdles, compounded by 30% of SDSs containing hazard warning inaccuracies. Fragmented databases and evolving regulations demand real-time updates, yet many lack centralized systems. Cultural narratives and evolving regulations demand real-time updates, yet many lack centralized systems. Implementing comprehensive chemical safety protocols and leveraging technology can help address these issues. Additionally, advancements in AI Entertainment are increasingly being utilized to improve safety data management and automate updates.
Additionally, understanding compliance requirements can be difficult, with some workers struggling to interpret safety protocols. Communication gaps, language barriers, and inconsistent training further heighten risks. Proper training and resources are essential to navigate the complexities of chemical safety management successfully. A thorough understanding of chemical hazard management strategies can significantly improve safety outcomes.
The Role of Proper Chemical Labeling and Documentation
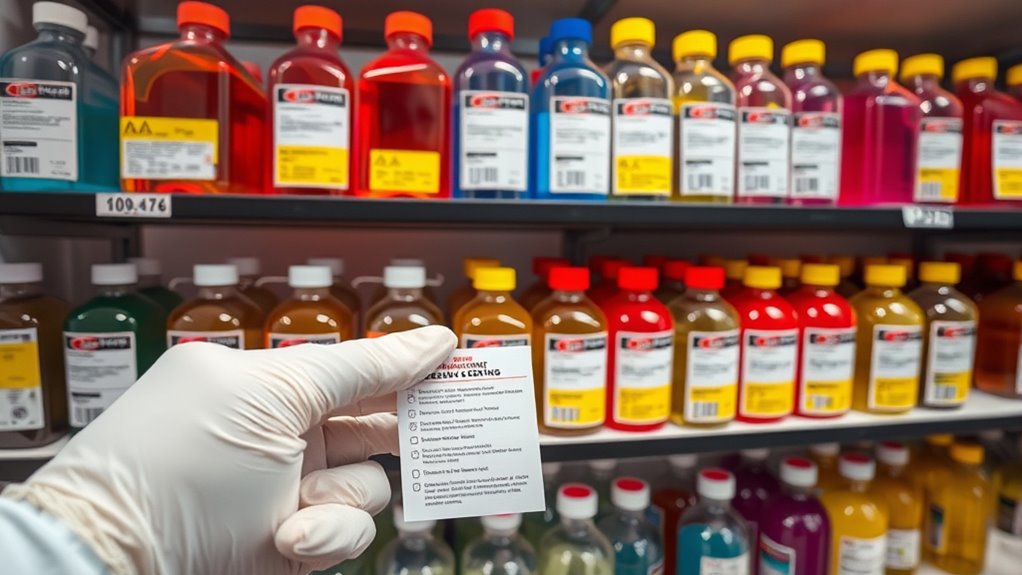
Proper chemical labeling and documentation are essential components of workplace safety because they guarantee that all chemical hazards are clearly communicated to everyone handling or exposed to these substances.
When labels meet OSHA and GHS standards, they include vital information such as hazard symbols, signal words, and precautionary statements, ensuring quick understanding of risks. Accurate labels display product identifiers, supplier details, and hazard pictograms, helping you recognize dangers immediately.
Maintaining labels and replacing worn-out ones prevent misidentification. Proper documentation, like Safety Data Sheets, aligns with labels and provides detailed safety procedures.
Clear, consistent labeling reduces exposure risks, facilitates emergency responses, and ensures regulatory compliance. You can considerably improve safety and minimize handling errors by prioritizing proper labeling and thorough documentation in your workplace.
Impact of Training on Regulatory Compliance
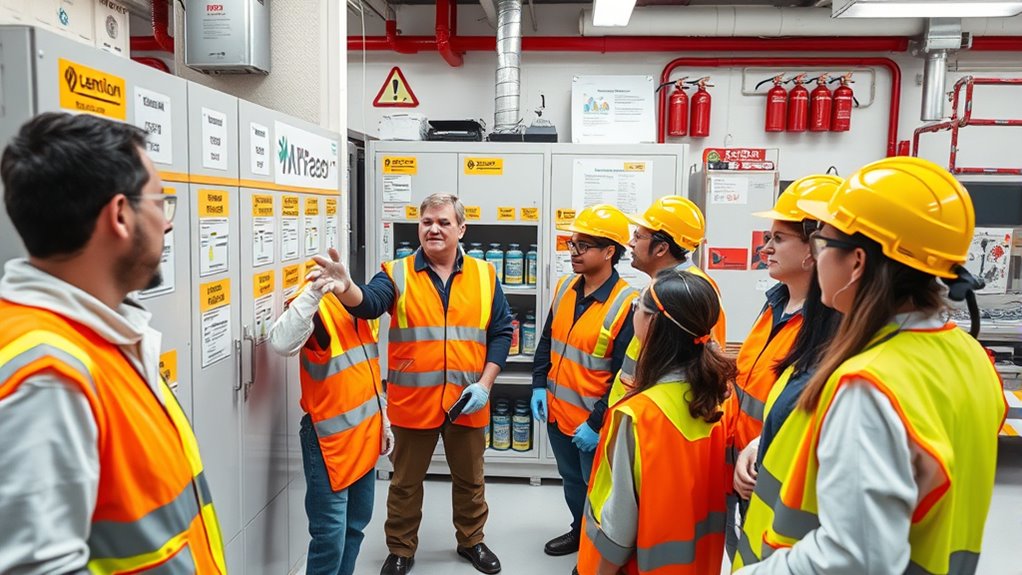
Effective chemical labeling and documentation set the foundation for workplace safety, but ongoing training amplifies their impact by ensuring everyone understands and follows these standards. When you stay current on OSHA HazCom updates, you reduce violations and avoid costly penalties by maintaining inspection-ready practices.
Proper training helps you accurately track hazardous chemicals, ensuring compliance with TSCA reporting deadlines like March 1, and prevents misclassification errors in SDSs aligned with GHS standards. It also streamlines inspections, making documentation readily available and preparing you for EPA audits.
Additionally, training demonstrates due diligence, limiting legal liabilities in chemical exposure cases and meeting international standards like REACH. Ultimately, well-trained staff helps you manage risks more effectively, lowering injury rates, environmental hazards, and long-term health costs while ensuring your facility remains compliant with evolving regulations.
Strategic Allocation of Safety Resources
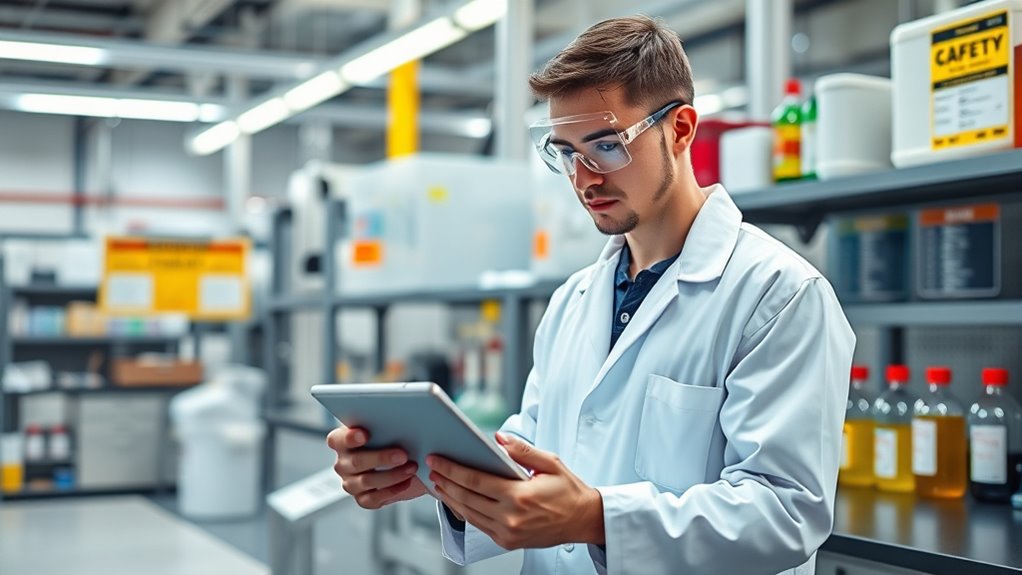
Strategic allocation of safety resources guarantees that your chemical safety program delivers maximum impact without overspending. By leveraging cost-effective methods like micro-learning and on-demand resources, you assure training remains effective while reducing expenses.
Making safety information easily accessible boosts resource efficiency and encourages employee engagement, especially when training is relevant and location-specific. Incorporating blended learning models and digital tools enhances accessibility and keeps employees involved.
Focused modules on specific hazards optimize learning time and resource use, while ongoing assessments help identify areas needing attention. Additionally, involving experienced staff in training leverages existing knowledge.
Conducting thorough needs assessments and aligning training with regulations ensures resources target real risks. This strategic approach guarantees your safety efforts are both efficient and impactful.
Ongoing Needs for Effective Chemical Safety Education
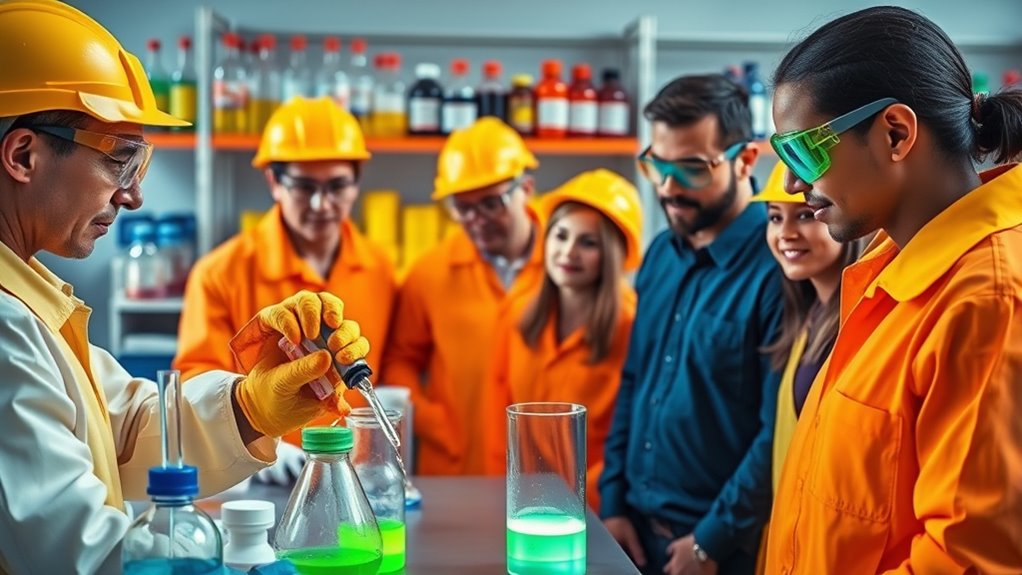
Despite existing safety protocols, ongoing gaps in chemical safety education continue to pose significant risks in academic and laboratory settings. You need to recognize that 35% of STEM/CTE teachers lack formal safety training, increasing the likelihood of accidents. Skipping safety tests or allowing non-perfect scores means students may not fully understand hazards, risking injury.
Systemic issues, like 58% of schools unaware of safety inspections and 41% conducting outdated chemical inventories, further weaken safety measures. Historical data shows 261 lab incidents causing injuries and fatalities, highlighting persistent dangers.
To improve, you should advocate for mandatory annual safety training, enforce safety test completion, and implement digital SDS management. Smaller class sizes and integrating safety modules early in curricula will help build a safety-conscious culture in educational settings.
Frequently Asked Questions
How Can Companies Measure Long-Term Improvements From Chemical Safety Training?
You can measure long-term improvements by tracking safety metrics like fewer OSHA-recordable incidents, reduced workers’ comp claims, and better audit scores.
Use employee feedback through surveys and focus groups to gauge attitude shifts.
Monitor on-the-job behaviors with checklists and workplace audits, and analyze near-miss reports.
Over time, these indicators show how well safety practices stick and how effectively training influences ongoing compliance and risk reduction.
What Are the Most Common Barriers to Implementing Safety Changes Post-Training?
You face several barriers when trying to implement safety changes after training. Limited budgets mean you might lack proper PPE or updated SDSs. Staff shortages and time constraints hinder follow-up and inventory updates.
Institutional issues like unclear procedures and weak leadership can slow progress. Additionally, language barriers, low engagement, and resistance to change reduce effectiveness.
Overcoming these obstacles requires prioritizing safety, streamlining processes, and fostering a safety-first culture.
How Does Training Impact Chemical Incident Response Times?
Imagine you’re steering a stormy sea; quick, accurate responses can prevent disaster. Training sharpens your ability to react swiftly, reducing chemical incident response times.
Data shows that after training, safety improvements and hazard communication efforts increase markedly, enabling you to act faster during emergencies.
With better access to safety data sheets and practiced procedures, you’re more prepared, helping you to contain incidents efficiently and prevent escalation.
What Role Do Employee Feedback and Engagement Play in Safety Training Success?
You play a critical role in safety training success through your feedback and engagement. When you actively share your insights and concerns, you help identify gaps and improve training methods.
Your involvement fosters a safety-focused culture, encouraging others to participate. This collaborative effort leads to better understanding, stronger safety practices, and fewer incidents.
How Frequently Should Chemical Safety Training Be Updated for Maximum Effectiveness?
You should update your chemical safety training regularly to stay compliant and guarantee maximum effectiveness. OSHA recommends initial training before exposure, with updates for new substances by July 2026, and for mixtures by July 2027.
Incorporate micro-learning and refresher courses periodically, especially after hazard changes or process updates. Annual reviews and on-demand resources help reinforce knowledge, while documentation ensures compliance during inspections.
Stay current to protect your team and meet regulatory standards.
Conclusion
By prioritizing chemical safety training, you reveal the secret to eliminating accidents and safeguarding lives—turning your workplace into an impenetrable fortress of safety. When every worker is empowered with knowledge, risks vanish like shadows at dawn. Don’t underestimate the power of proper labeling and ongoing education; they’re your ultimate weapons against catastrophic incidents. Embrace extensive training now, or risk facing chaos, fines, and irreversible harm—because safety isn’t just a priority; it’s your entire future.